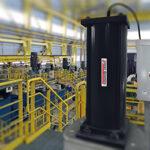
Cowan Dynamics
This article has been reviewed by Cowan Dynamics Application Engineering team. Contact Us and our application engineers will assist you with your application.
What is a ball valve?
Ball valves are rotary or quarter-turn valves. Their closing membrane is a bored pivoting ball that is supported on one or both top and bottom ends. When the valve is open, the bore in the ball is aligned with the flow of the pipeline, allowing the substance to pass through. When closed (by turning the stem 90 degrees), the bore becomes perpendicular to the flow and stops it. These ball valves can have resilient or metal seats, are usually bi-directional and come in different connection configurations. The most common ball valve configuration being flanged and threaded.
Ball Valve Design
Conventional ball valves are designed primarily for fluid isolation as they have poor control characteristics. The seat and body of a ball valve can be easily eroded if the valve is not fully closed or opened. Ball valves can also be designed for flow control. When designed for control they have a special feature in the design of the bore of the closing membrane. This bore is shaped as a “V” and with this design, they are called “V-port” ball valves.
This design allows for linear and even equal percentage flow characteristics. When the valve is in the closed position and opening begins, the small end of the “V” opens first allowing stable flow control during this stage. This design is made of a robust construction to handle higher fluid velocities which could normally damage a standard valve. When properly machined, the V-port ball valve can be used as a control valve, offering a tight shutoff.
Ball Valve Applications
Ball valves are widely used in many industrial process applications. Conventional ball valves are mostly used for fluid isolation when fast operating times and tight shut-off are necessary or critical. They can also be used as “full port” without restrictions when needed. The ball valve is typically used in the oil and gas industry and are found in many sectors of manufacturing, chemical storage, and even residential uses.
Ball Valve Advantage
- In small sizes, they can be compact and low-maintenance.
- Cost-effective compared to other types of valves.
- Seat design provides excellent sealing capability.
- They open and close quickly, ideal as emergency shut down valves (ESD)
- Ball valves have the design flexibility that allows for multiple pathways, multiport valves
Ball Valve Disadvantage
- Conventional ball valves are not suitable for flow control since throttling can cause the seat of a ball valve to erode quickly.
- For slurry applications or fluids with a high percentage of solids, particles collide with the ball valve surface and can adhere to them. This can cause leakage, abrasion, and other problems.
- In large sizes, they have a complex design, and maintenance can be time-consuming.
Ball Valve Actuators
Ball valves, as any other type of valve, requires an energy source to be operated. The energy required depends mainly on the design and the pressure differential across the valve. Ball valve actuators can be selected depending on the source of power (hydraulic, pneumatic, electric, etc.) to the actuator.
When pneumatic pressure is available, ball valve actuators can be:
Rack and Pinion Valve Actuator, for double and single acting
Scotch-Yoke Actuator, for double and single acting
When hydraulic pressure is available, ball valve actuators can be:
Hydraulic scotch Valve Actuator, for double and single acting
When electric power is available:
Electro-hydraulic Rotary Actuator for double and single acting, Conventional full or reduced port ball valves (ON/OFF)
Electro-hydraulic Actuator for double and single acting, V-ported or segmented ball valves (Control/modulation)
When using the process gas pressure,
Gas & Oil Rotary Actuator for double and single acting