E2H-ESD SeriesElectro-hydraulic Emergency Shut-off Valve Automation
Self-contained system engineered for fast, safe, and reliable failure conditions on the loss of power and/or ESD signals.
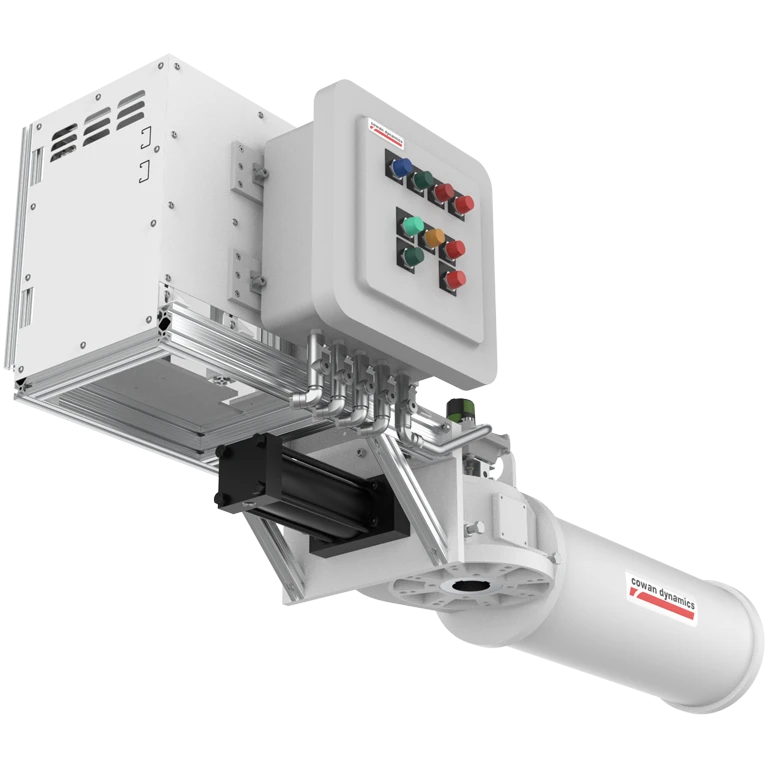
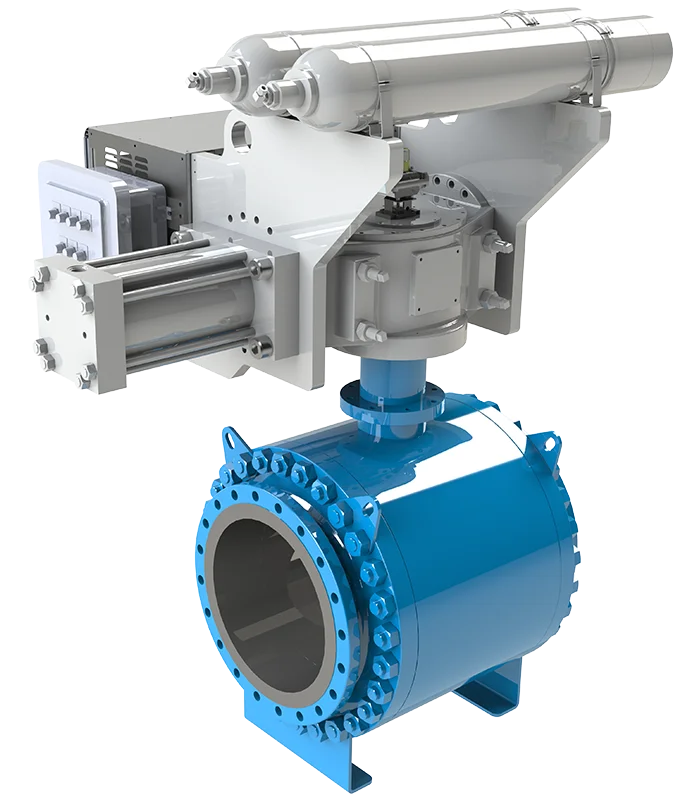
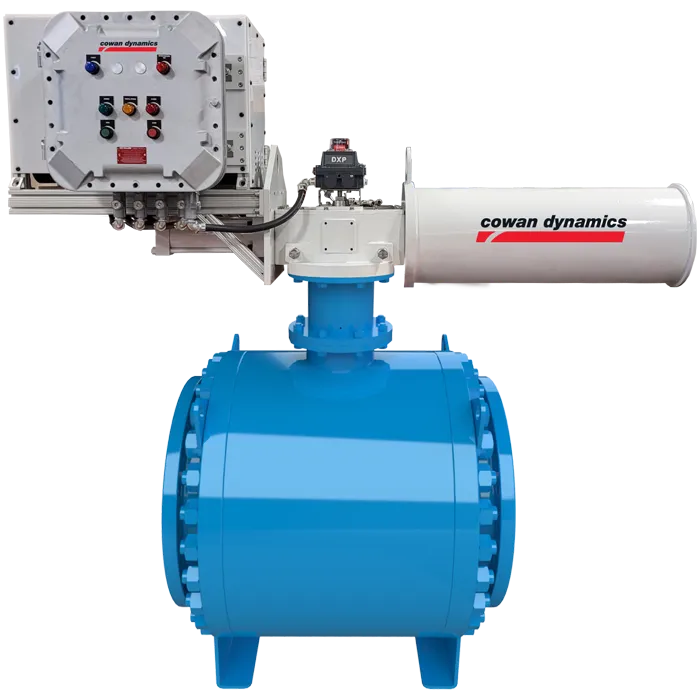
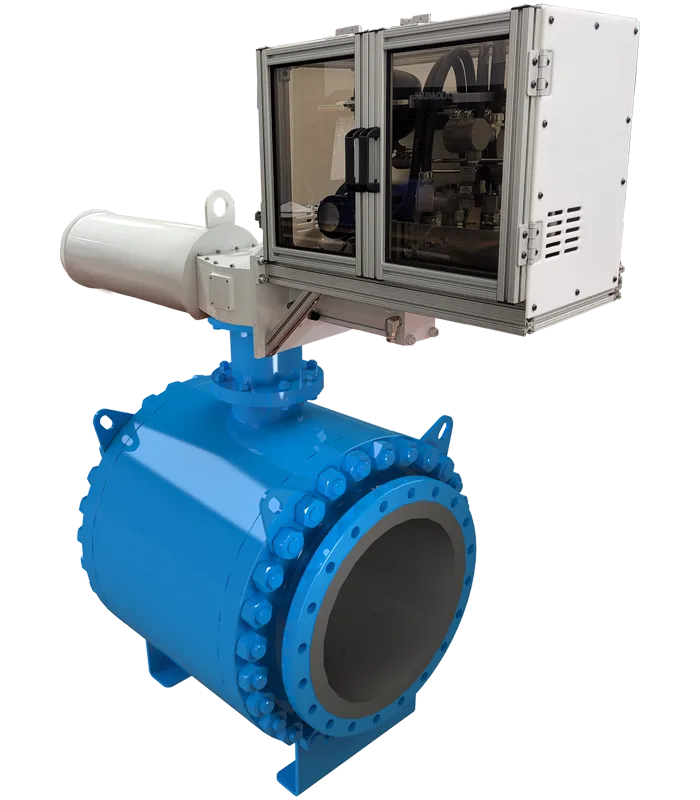
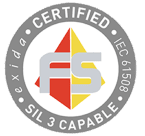
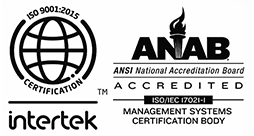
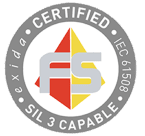
Specifications
Design |
Fully modular design
|
---|---|
Torques | up to 3,000,000 in-lbs |
Service Mode |
On/Off Service, Emergency shutdown valves (ESD). Option for modulation is available.
|
Control Method | Local and remote control |
Indications | Visual position indicators |
Design | Explosion-proof design |
SIL Rating |
SIL (Pending)
|
Response Speed | Fast acting Acting |
Fail Modes | Fail Last, Fail Close, or Fail Open |
Operating Pressure | Up to 2,500 psi |
Valve Testing Method | Partial Stroke Test (PST) |
Overrides | Manual Override, Hydraulic hand pump |
Certifications | ETL Certified to CSA / cUL / ATEX Electrical Requirements |
Service | On/Off – Emergency Shutoff |
---|---|
Ambient Temperature rating | Standard – (-20C to +40C) High – (-20C to +55C) Low – (-40C to +40C) Standard HMI – (0C to +40C) Low Temp HMI – (-30C to +40C) |
Environmental Protection | NEMA 4X/IP66 |
Hazardous area classifications | Class 1, Division 1, Gr C&D (CSA/cUL) General purposes (CSA/cUL) ATEX, II 3G EEx nA II T3 -40°C ≤ Ta ≤ 65°C, Tamb ≤ 65°C |
Max available torque | 3,000,000.00 Lbs-in Hydraulic output 306,000.00 Lbs-in Spring output |
Certifications | SIL-3 (Pending) CSA/UL/ATEX, Electricals Province CRN as applicable for accumulators |
Partial stroke | Standard – 3rd limit switch, set position Smart option* – Configurable to any position from 0% to 100% |
Duty Cycle | Standard – On/Off Applications Smart option*- Inverted duty motor – Continuous duty, Variable speed |
Conduit Entries | Four (4) bottom ½” NTP entries |
Rotary Valve Types | Ball Valve, Butterfly Valve, Plug Valve, etc. |
Common Applications | Conventional, gas storage, HP/HT Wells. Pipelines, tank farms and others |
Common Terms | Surface safety valve, safety shutoff valve, emergency shutdown valve (ESDV), hydraulic shutdown valve, shutdown valve (SDV), emergency shutoff valve |
Voltage | Phase | Hz |
---|---|---|
120VAC | 1 | 50/60 |
240VAC | 1 | 50/60 |
115VAC | 1 | 50 |
460VAC | 3 | 60 |
575VAC | 3 | 60 |
208VAC | 3 | 60 |
Local Operation | Standard Display: • Power/Overload/Open/Closed PST light indicators • Open/Close/push buttons Smart Display* • Multi-colour HMI touch screen |
---|---|
Remote Operation | Standard Inputs: • Discrete Open/Close/PST/ESD signals Standard Outputs • Discrete open/close limit positions Smart Inputs* • PST signal- 4-20mA positioning Smart outputs* • Programable PLC, 4-20 mA position feedback |
*Smart display | Available only for general purposes application and at operational temperature range of -30C to +40C |
Operating Temperatures | -50°C to 40°C |
---|
Highlights
The hydraulic power module of the E2H-ESD contains all hydraulic components to transform the supplied electric energy into the required hydraulic power supply.
In E2H-ESD series actuators, all hydraulic components and sensors are integrated into a compact manifold block. This results in space saving, ease of installation and elimination of leaks and break points by removing all hoses which leads to reduction in down time required for service.
Standard units offer an explosion proof pump-motor assemblies for on/off operation, options for inverter motor for variable speeds available for control applications.
Designed to compensate inherent hydraulic leakage through the components to minimize pump operation.
Design & Materials
Click on the (+) Icons to see more details.
Single-Acting Spring-Return
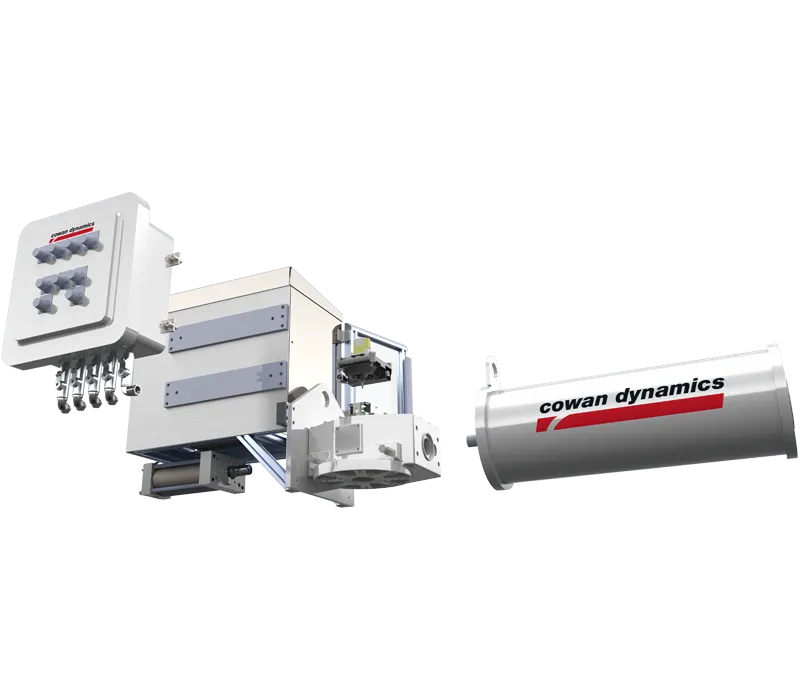
Control System Module | Local/Remote controls Module: Can be mounted directly on the unit providing a self-contained compact design or remotely in cases where the unit cannot be accessed easily due to installation or environmental conditions.
Hydraulic Power Module
Spring-canister Module | Fully sealed compact canister, all welding is certified to CSA 47.1 Division 2. This spring canister is also fully modular and field-replaceable.
Scotch Yoke Module | Symmetrical units completed with +/ - 5% mechanical travel stops, local visual indicators, and a rotary beacon with position feedback for end-to-stroke and partial stroke set points
Hydraulic Cylinder Module
Single-Acting with Accumulators
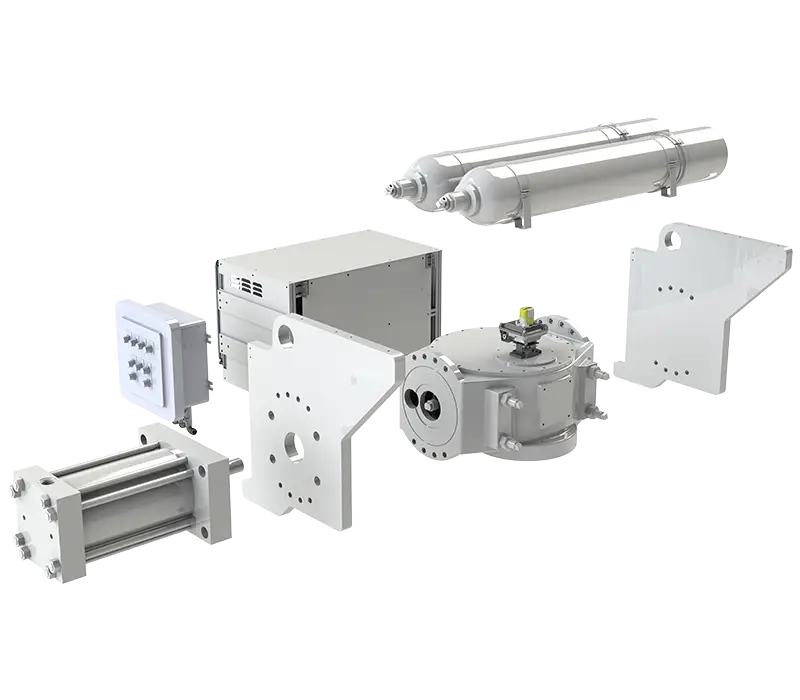
Control System Module
Hydraulic Power Module
Accumulators Module
Scotch Yoke Module
Hydraulic Cylinder Module
Hydraulic Power Module
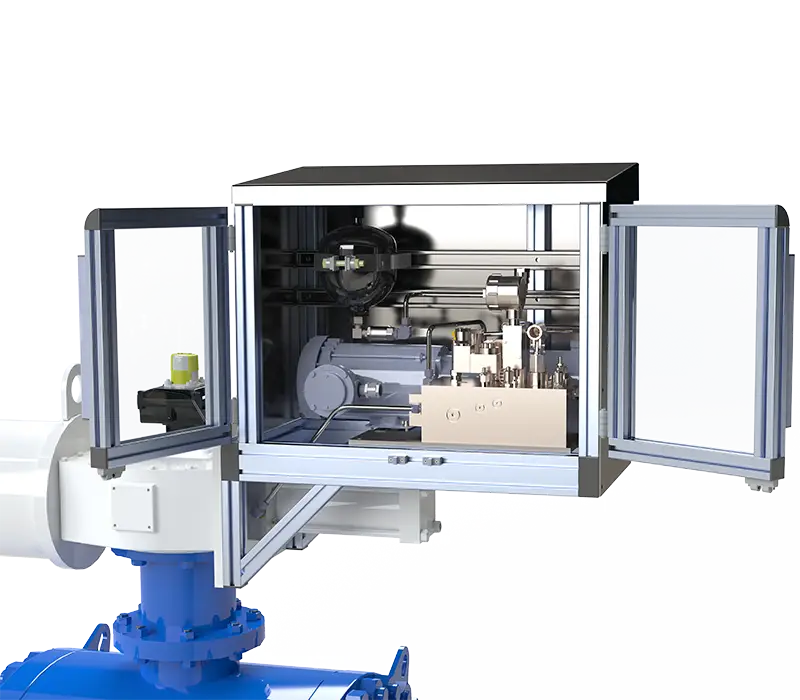
Hydraulic compensation accumulator - Ensures no changes in the hydraulic system due to thermal expansion.
Enclosure frame - Even when all components within this module are rated for hazardous areas the module is fully enclosed and pad-lockable for additional protection to environmental conditions and operator's safety.
Manifold block - All hydraulic components and sensors are integrated into a compact manifold block. Fast failure or safe position speeds are achieved by an exchangeable secondary tamperproof manifold designed for the required speed.
Hydraulic pump & electrical motor
E2H-ESD Applications
Industries trust us to provide state-of-the-art actuation and automation solutions in the following sectors.
Oil and Gas
Empowering oil and gas operations with advanced valve automation, ensuring efficient flow control for upstream and downstream applications.
Chemical Processing
Maximizing chemical processing efficiency with cutting-edge automation and precision control technologies.
Mining & Processing
Boosting mineral processing productivity with innovative automation and control systems, like our dart valve automation products.
Water Treatment
Streamlining water treatment processes with advanced valve automation, such as regulating flow rates for precise flow control.
Power Generation
Enhancing power generation reliability through state-of-the-art valve automation, ensuring seamless operation of turbine control valves for optimized energy output.
Manufacturing
Revolutionizing manufacturing efficiency with precise actuation automation by optimizing the operation of advanced operations from aviation testing systems to industrial milling process control.
Datasheets & Videos
Introducing the new Cowan Dynamic’s E2H-ESD. From our line of Electrohydraulic actuators (E2H), this unit has been specifically designed to operate emergency shut-off valves (ESDV).
Understanding how crucial ESD valves are for the safe operation of piping systems, the E2H-ESD actuator provides fast, safe, and reliable failure conditions on loss of power and/or ESD signals. The E2H-ESD emergency shut-off valve actuator is designed to operate in hazardous areas and under extreme conditions.
What is an ESD Valve?
Emergency shutoff valves (ESD valves) are specifically designed to shut the process, often carrying hazardous media, in the case of an undesirable event. For this reason, they must be actuated to automatically respond to a signal triggered by such an event. They are key components in a safety instrument system providing protection to operators and the environment.
Where are ESD valves most used?
These valves can be found mostly in the oil and gas industry, installed in pipelines, production wellheads or tank farms. Typically, they are in very remote locations where sources of energy are limited or not available. These valves are critical to process safety and need a reliable self-powered automatic shutdown system.
The E2H-ESD actuator is a reliable and energy efficient equipment that combines the precision and large force capacities of hydraulic systems with the convenience and availability of electric power. Designed to operate any type of rotary valves in hazardous areas under extreme conditions, this actuator has been tested and certified to meet requirements under the CSA Group for its electrical components and in conformance with requirements under IEC 61508 standard to meet its safety integrity level.
In the E2H-ESD actuators, all hydraulic components and sensors are integrated into a compact manifold block. This results in space saving, ease of installation and elimination of leaks and break points by removing all hoses which leads to reduction in down time required for service.
Units come standard with components certified to Explosion proof under hazardous area classifications, even when all components within this module are rated to hazardous areas the module is fully enclosed and pad-lockable for additional protection to environmental conditions and safety to operators
The E2H-ESD uses a hydraulic cylinder from Cowan’s own series of heavy – duty 3000 psi rated linear actuator, ML.
To ensure a safe and reliable failure condition regardless of the operation status, the power-fail-safe model of the E2H-ESD is completed with a spring that is fully sealed in a compact canister, all Welding is Certified to CSA 47.1 Division 2.
The electrical control panel comes standard mounted directly on the unit providing a self- contained compact design ready to be used. When required, the panel can be mounted remotely in the areas where the unit cannot be accessed easily due to installation, environmental conditions, etc. Moreover, to provide cost savings and ease of status monitoring for operators in case of multiple actuators, a central control panel can be mounted remotely to control multiple units.
Designed to be energy efficient, In the E2H-ESD Series actuators the motor stops when there is no movement required from the valve, this leads to very low power consumption and increased life of moving components.
Understanding that emergency shut off valves are critical parts of safety systems and therefore a reliable actuator is a must, the design of the E2H-ESD is a non-complex (Type A) component based on the definition of IEC 61508 (device with well-defined failure modes, well known failure rates, and behavior under fault conditions that can be completely determined), for which has a Safety Integrity Level of 3. Components which are in effect in the fail-safe function are all SIL certified.
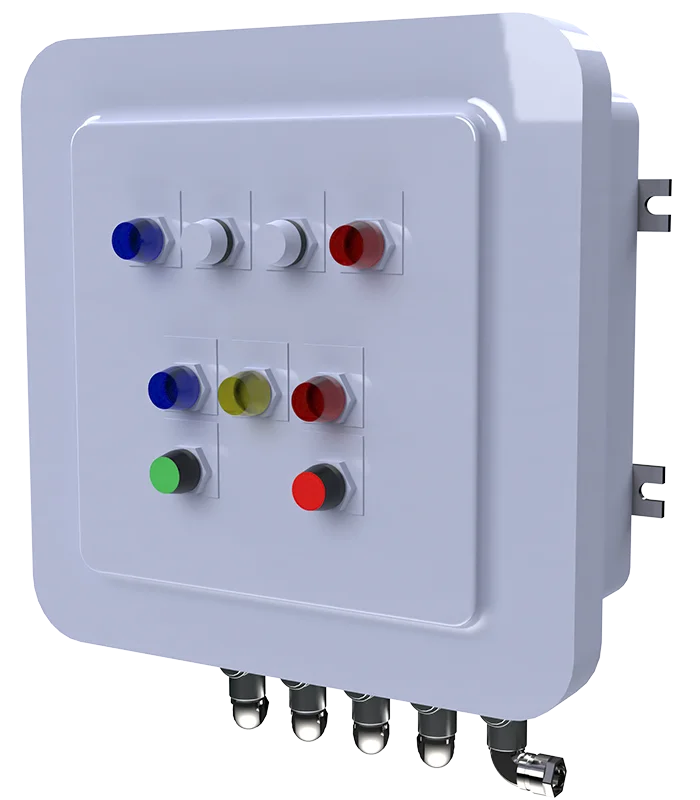
Control System Module
The electrical control panel can be mounted directly on the unit providing a self- contained compact design leading to space saving. When required, the panel can be mounted remotely or in addition to the local integrated panel a remote station with control panel can be added in the areas where the unit cannot be accessed easily due to installation or environmental conditions. Moreover, to provide cost savings and ease of status monitoring for operators in case of multiple actuators, a central control panel can be mounted remotely to control multiple units. Push buttons and LEDs are available on the electrical control panel for sending local commands and quick status monitoring.
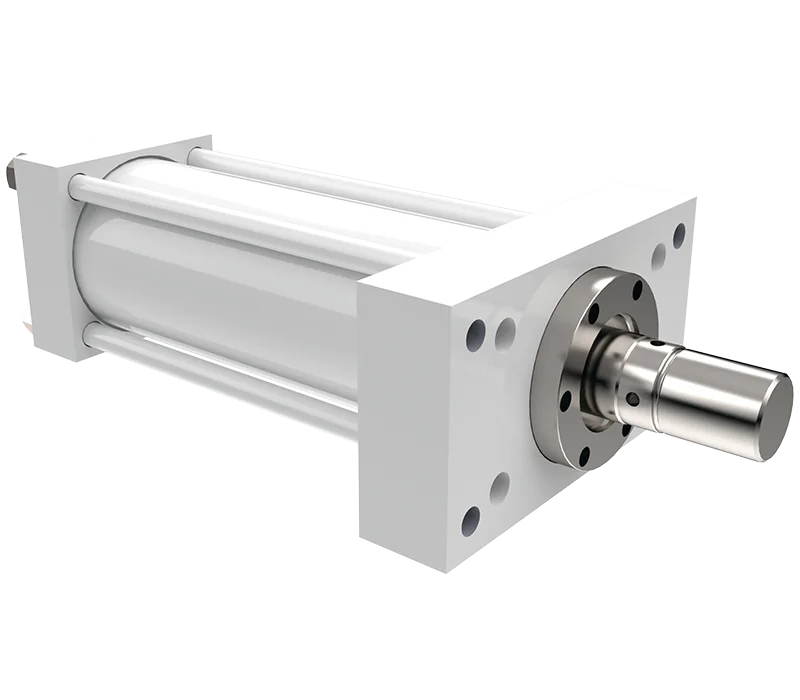
Hydraulic Cylinder Module
The E2H-ESD uses a hydraulic cylinder from Cowan’s own series of heavy – duty 3000 psi rated linear actuator, ML, to transform the hydraulic energy provided by the hydraulic power module into thrust. This cylinder is also fully modular and field replaceable.
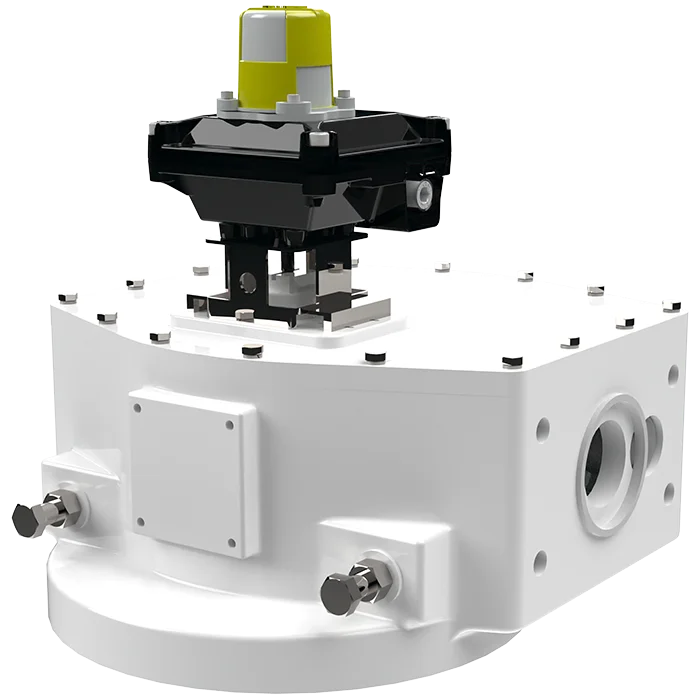
Scotch Yoke Module
The E2H-ESD uses a Scotch Yoke mechanism to transform the output thrust from the hydraulic cylinder into torque to actuate the rotary valve. This module is completed with mechanical travel stops and a rotary beacon with position feedback for end-to-stroke and partial stroke set points. This Scotch Yoke mechanism is also fully modular and field replaceable.
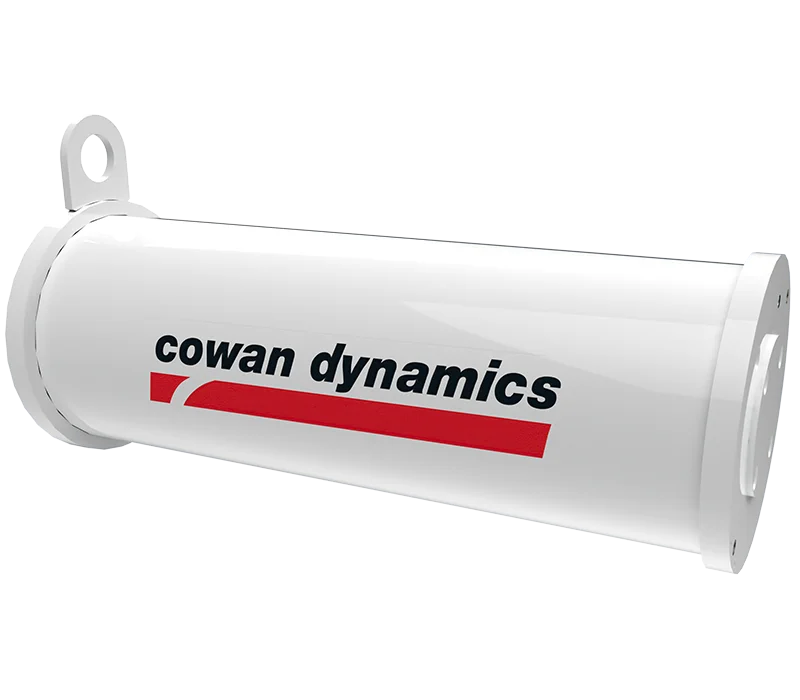
Spring-canister
To ensure a safe and reliable failure condition regardless of the operation status, the power-fail-safe model of the E2H-ESD is completed with a spring that is fully sealed in a compact canister all Welding is Certified to CSA 47.1 Division 2. This spring canister is also fully modular and field replaceable.
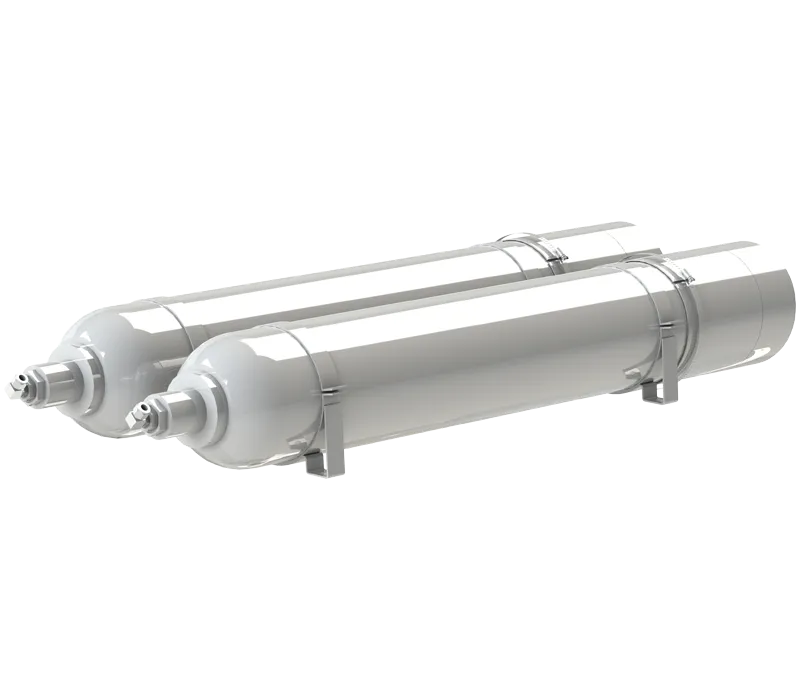
Accumulators
To ensure a safe and reliable failure condition regardless of the operation status, the power-fail-safe model of the E2H-ESD is completed with hydraulic accumulators for its D06 to D08 modules. Accumulators hold a Canadian registration numbers (CRN) and are installed directly on the unit or remotely depending on customers requirements and models.
Comparison Table
E2H-ESD
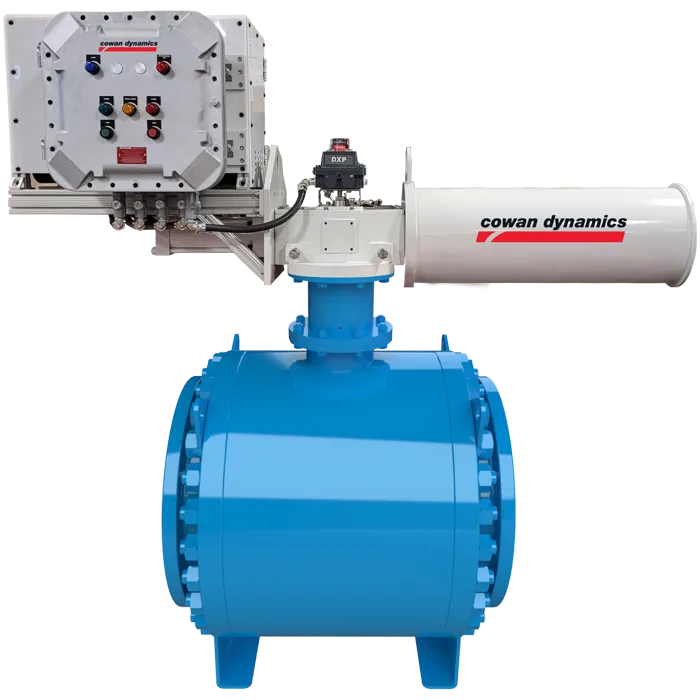
E2H90
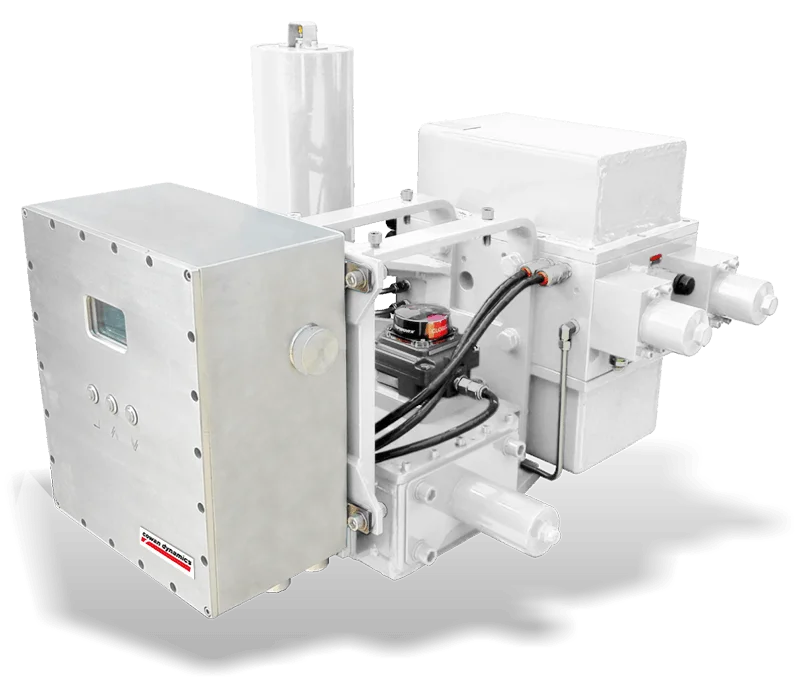
Actuator mechanical Design
Scotch Yoke
Scotch Yoke
Failure system
Spring return, fully sealed in a compact canister. Welding’s Certified to CSA 47.1 Division 2. Option for hydraulic return on preloads higher than 306,000 lbs.-in
Hydraulic accumulators system designed to 2 strokes. Option for spring is available
Fail Function
Fail on Loss of power & ESD Signal
Fail on Loss of ESD Signal
Operational ambient temperature rating
(-50C TO 40C)
(-40C TO 70C)
Control Panel
Standard: Installed on the unit wired and tested Option: Remote
Standard: Installed on the unit wired and tested Option: Remote
Interface
Standard-Power/Overload/Open/Closed & PST light indicators. Open/Close/push buttons Option: HMI-Multi Color Touch Screen (only available with the smart printed circuit board option)
Standard LCD Screen, printed circuit board. Navigation buttons, Open/Close buttons. Local, Remote selector
Communication
Standard: Discrete. Open/close/ESD/PST Option: Smart PCL, 4-20ma control, 4-20 ma c/w HART, PROFIBUS,PROFINET.
Standard: Discrete. Open/close/ESD/PST
Environmental Protection
NEMA 4X, IP66
IP67
Hazardous Area classification and certifications
CSA or uL or cUL CI1,Div1&2,Gr C&D OR AATEX, II 2G EEx d IIB
Ex d IIC T6
Power Supply Voltage
120VAC/60Hz/Single phase. Other options available.
220VAC/50Hz/Single phase. Other options available.
Manual Override
Standard: Manual Hydraulic pump
Standard: Manual Hydraulic pump
Partial Stroke
Comes standard, set at a set position. Standard 20% open. Speed adjustable
Comes standard, set at a set position. Standard 20% open
Fail safe time
Fast- Less than 15 secs for all models. Adjustable and padlock able
Standard : Fixed. Not adjustable. Option: Adjustable, not lockable
Stroke operation
Directly driven by the hydraulic pump. No down time, recharge not needed
Driven by the pressurized fluid in the accumulators. Accumulators sized to 2 strokes, after this accumulators must recharge
Recharge time
Not required. Unit is always available to stroke the valve
Between 15 to 30 mins depending on the model
Modular Design
Yes, Controls and hydraulics can be provided remotely mounted as a standard design if required
No
Hydraulic Design
All Hydraulic components and sensors are integrated into a compact manifold block. The complete hydraulic system is Fully enclosed and pad-lockable
All hydraulic valves are included in a enclosed cabinet, interconnection between components is all done with stainless steel tube and fittings.
Mechanical travel stops
Mechanical travel stops +/- 5% and local position indicator
Mechanical travel stops +/- 5% and local position indicator
SIL Certification
SIL 3 (Pending)
SIL 2 (HFT)=0 ; SIL 3 (HFT>=1)
Lifting lugs
Yes
Yes