Emergency Shutdown Valve SystemZE-ESD Module
Zero-Emission Emergency Shut-down (ESD) for valves that require an automatic fail-safe position in locations where power is not available and fugitive emissions not permitted.
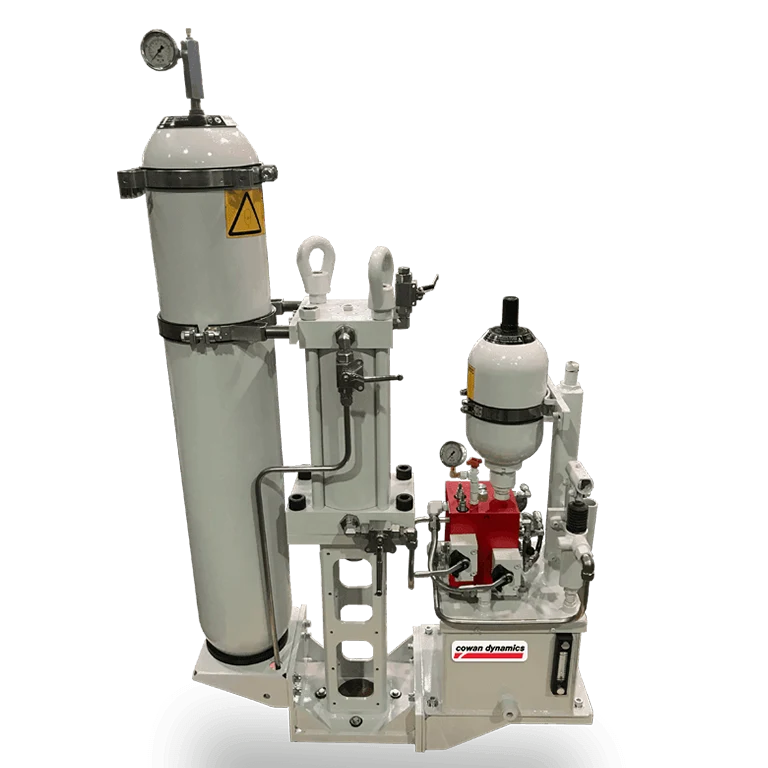
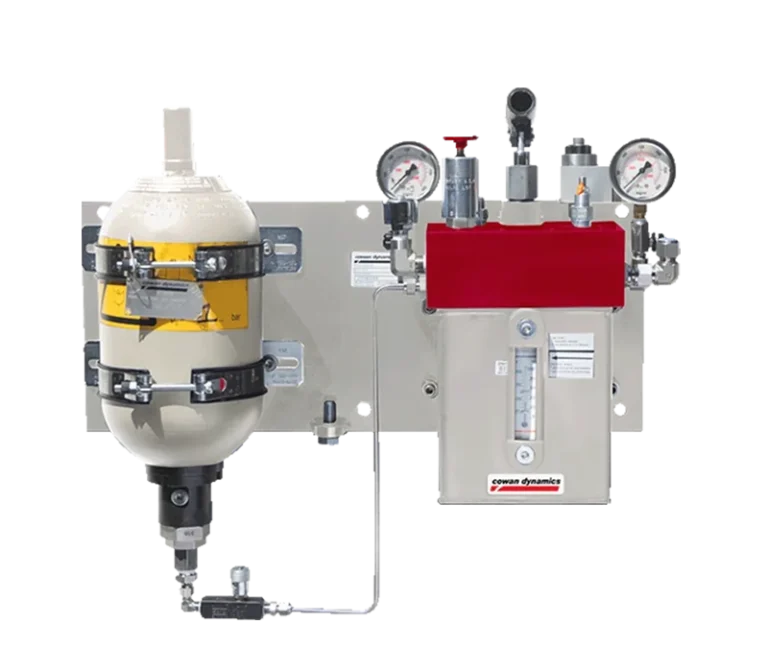
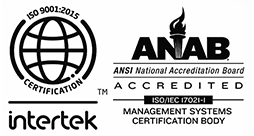
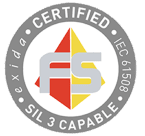
Specifications
Designed for all linear and 1/4-turn actuators
Service | Emergency Shutdown Valve System |
---|---|
Ambient Temperature rating | -50° to + 40° C |
Pump working pressure | 1,500 PSI-g |
Certifications | Province CRN as applicable |
Linear Valve Types | Knife Gate Valve, Gate Valve, Globe Valve, Pinch Valve, etc. |
Rotary Valve Types | Ball Valve, Butterfly Valve, Plug Valve, etc. |
Common Applications | Conventional, gas storage, HP/HT Wells. Pipelines, tank farms and others |
Common Terms | Surface safety valve, safety shutoff valve, emergency shutdown valve (ESDV), hydraulic shutdown valve, shutdown valve (SDV) |
Highlights
This self-contained Emergency Shutdown (ESD) module can be used with rotary or linear valves and consists of a hydraulic manifold block, a leakage compensating accumulator, an oil reservoir, and hydraulic control components.
In normal operation the system holds the valve in its “normal” or “operational” position locked in place.
These systems are engineered by Cowan to be retrofitted onto existing pipelines without taking the valve out of service.
Cowan’s ZE-ESD Module is a self-contained Hydraulic Emergency Shutdown System (ESD) to automate valves that require a fail-safe position in locations where power is not available.
In the event of a failure, triggered by an ESD signal, the system will use stored hydraulic pressure or a pre-compressed spring to move the valve actuator to the desired fail-safe position (open or close) ensuring an automatic fail-safe system without the need for external power.
This system is designed to minimize maintenance and is engineered for tough heavy-duty industrial applications to operate valves with high thrusts and torques.
Design & Materials
Click on the (+) Icons to see more details.
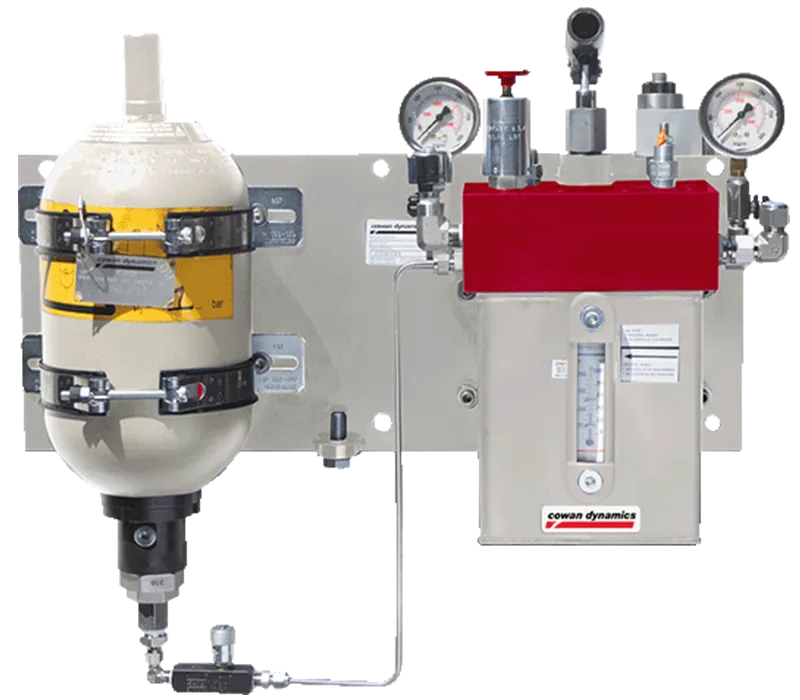
Hydraulic Bladder Accumulator | To compensate for leakage in the hydraulic system
Manual Hand Pump | To manually return the valve to its "operational" position and re-arm the system
Hydraulic Control Manifold | Includes manual and/or solenoid operated directional valves, flow controls and pressure gauges.
Hydraulic Oil Reservoir | Designed to contain the amount of hydraulic fluid required by the system.
ZE-ESD Applications
Industries trust us to provide state-of-the-art actuation and automation solutions in the following sectors.
Oil and Gas
Empowering oil and gas operations with advanced valve automation, ensuring efficient flow control for upstream and downstream applications.
Chemical Processing
Maximizing chemical processing efficiency with cutting-edge automation and precision control technologies.
Mining & Processing
Boosting mineral processing productivity with innovative automation and control systems.
Water Treatment
Streamlining water treatment processes with advanced valve automation, such as regulating flow rates for precise flow control.
Power Generation
Enhancing power generation reliability through state-of-the-art valve automation, ensuring seamless operation of turbine control valves for optimized energy output.
Manufacturing
Revolutionizing manufacturing efficiency with precise actuation automation by optimizing the operation of advanced operations from aviation testing systems to industrial milling process control.
Datasheets & Video
About the ZE-ESD Module
The ZE-ESD Module integrated to an appropriate valve actuator is capable of achieving up to 118,000 Lbf or 131,000 in-lbs depending on the type of valve being actuated and subject to their size. Exposure to harsh conditions is another challenge that ESD valve actuators must withstand. Note, the ZE-ESD Module is only a hydraulic source and needs an actuator to produce thrust/torque.
For this reason, the ZE-ESD system has been engineered to operate in ambient temperatures as low as -50C and as high as +40C, with an environmental protection to IP66 and certified for use in hazardous areas.
How The ZE-ESD Valve System Works?
This self-contained ZE-ESD system can be used in conjunction with linear or rotary valve actuators and consists of a hydraulic manifold block, a leak-compensating accumulator, a small reservoir, and a hydraulic hand pump.
In normal operation, the system holds the valve in its “normal” or “operational” position, locked in place as it is connected to a double–acting actuator. No additional pressure or energy is needed to compress a spring. This design helps to reduce pressure losses, inspections, and costs.
In the event of a failure triggered by the ESD signal, the system will use the stored hydraulic pressure in the accumulator to move the valve to the desired failure position, ensuring a safe automatic system without the need for external power. This system is designed to minimize maintenance and is built for heavy–duty industrial applications to actuate valves with high thrusts and torques.
What is an ESD Valve?
Emergency shutoff valves (ESD valves) are specifically designed to shut the process, often carrying hazardous media, in the case of an undesirable event. For this reason, they must be actuated to automatically respond to a signal triggered by such an event. They are key components in a safety instrument system providing protection to operators and the environment.
Where are ESD valves most used?
These valves can be found mostly in the oil and gas industry, installed in pipelines, production wellheads or tank farms. Typically, they are in very remote locations where sources of energy are limited or not available. These valves are critical to process safety and need a reliable self-powered automatic shutdown system.
ESD Valve Systems Applications
This system is ideal for valves in remote locations that require a self-powered automatic failure position. This system utilizes hydraulic pressure to actuate the valve to the desired failure position in the event of an ESD signal loss which can be from pressure pilots, solenoid valves, switches, transducers, or others depending on the application. The ZE-ESD is compatible with emergency shutoff linear and rotary valve actuators such as gate valves, ball valves, butterfly valves, etc.
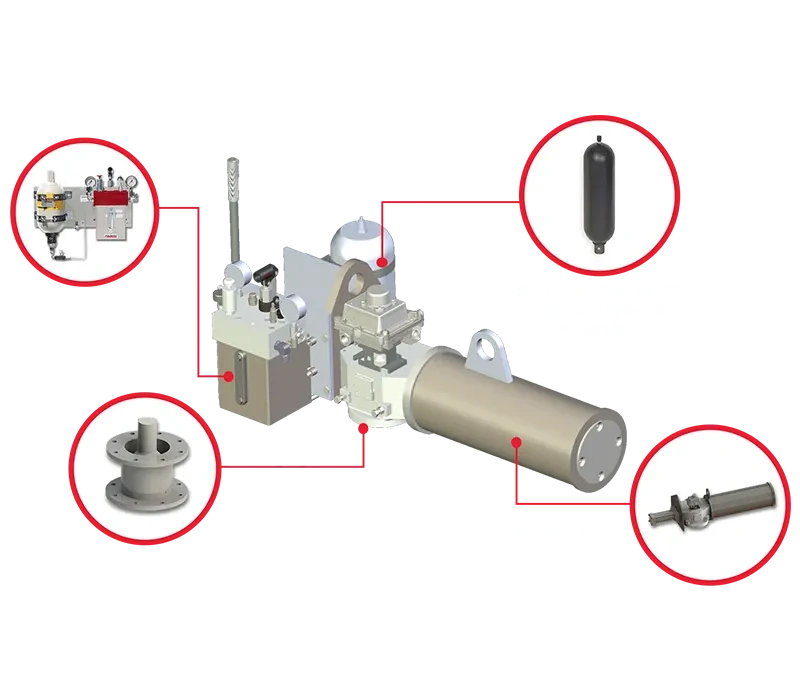
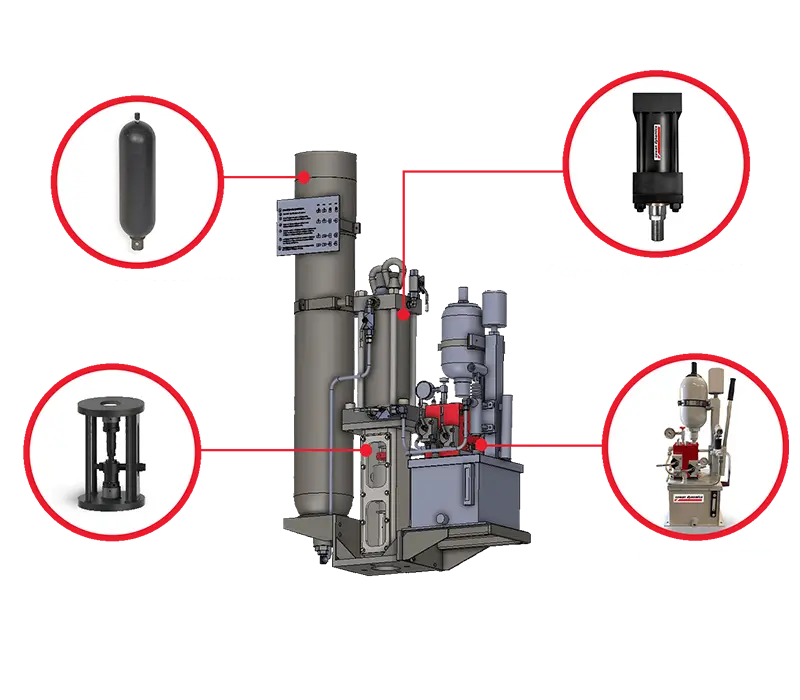