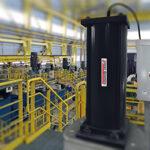
Cowan Dynamics
This article has been reviewed by Cowan Dynamics Application Engineering team. Contact Us and our application engineers will assist you with your application.
In this article you’ll learn to maximize mineral recovery in a flotation cell. Dart valves have traditionally been used as level control valves in flotation cells. The dart valve positioning in flotation cells requires high consideration as the goal is to maximize mineral recovery. For this reason a reliable and accurate control valve actuator is crucial.
Pneumatic actuators vs electro-hydraulic actuators for dart valve control
Traditionally dart valves use pneumatic actuators to control the flotation cell level. However, due to air compression or elasticity, this method of automation can cause problems in accurate and efficient level control. The thrust due to the pressures at the bottom of the cell acts against the movement of the actuator which can cause compression of the air inside the cylinder.
This effect leads to problems in actuator responses to control signals which negatively effect mineral recovery. If the actuator is not able to respond effectively to a close signal, the cell level will decrease beyond optimum levels which will reduce efficiency of the flotation cell. If, on the other hand, the actuator does not respond properly to an open signal, the cell level will rise beyond optimum levels which could overflow the cell and cause not only significant costs in material loss, but in cleaning, maintenance, and operating time. This malfunction of the dart operation also results in accelerated valve and actuator wear.
In applications where the loss of control due to air compression is a concern, the most appropriate solution is with the use of hydraulic actuators. Due to the non-elasticity of most fluids, it can be guaranteed that even when thrust forces are being applied to the actuator, the fluid being non-compressible will ensure that the valve is locked in its target position. The integrated solution to automate dart valves with hydraulic systems can be found in Cowan Dynamics’ E2H electrohydraulic actuators. Combining a linear hydraulic actuator and a self-contained power system with remote and local PLC controls, this solution ensures accurate, repeatable, and unalterable control due to process pressures in the cell. With a dead band of 0.1% of the stroke, the level and retention time of the slurry can be ensured in a more efficient way compared to pneumatic systems, which in the long term translates into increased production, reduced maintenance and operating costs due to unscheduled cell shutdowns.
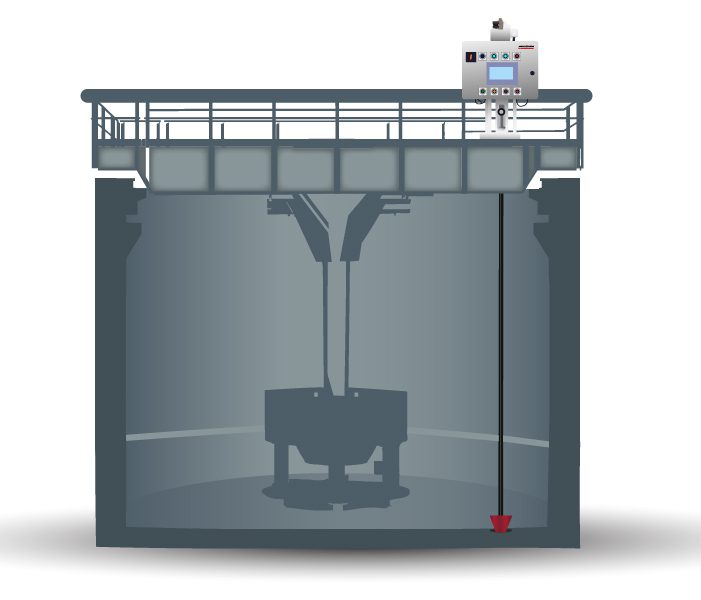
One of the most important factors when looking for alternatives to more efficient flotation cell management is energy consumption, understanding that, as in any process, the objective is to reduce the amount of energy needed to generate the final product. Pneumatic control systems, by the nature of their controls, are constantly consuming compressed air. This excess usage of the compressed air system can waste thousands of dollars of electricity per year. This not only wastes energy but it can also cause the compressed air system to lose pressure which reduces performance in other sections of the plant.
One of the advantages of E2H electrohydraulic actuators is that the electric motor only spins when the valve moves. Once the target position is reached the system hydraulically locks in place. This greatly reduces the energy consumption and operating costs of the dart valve level control system.
The control panels can be installed locally, self-contained to the actuator, or remotely with up to 13 valves operated by the same panel reducing space and installation costs. Because they are controlled by a PLC, E2H electrohydraulic actuators can be programmed to collect information on valve operation. This information can be sent to the central control system to be configured to adjust the actuator operation to respond to changes in the process conditions.