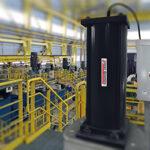
Cowan Dynamics
This article has been reviewed by Cowan Dynamics Application Engineering team. Contact Us and our application engineers will assist you with your application.
A valve is a pressure vessel with internal moving parts; and when they move, they encounter resistance from other parts and from the flow. The recording of the pressures and forces associated with overcoming these resistances can be referred to as “valve signature”. For actuator sizing, it is critical to obtain accurate valve thrust/torque data. This is especially true for spring-return actuators as conservative or exaggerated valve thrust/torque data can lead to extremely oversized and expensive actuators.
The thrust or torque required to move the valve, in either direction, will vary throughout its stroke. In industry, the following terms are used to describe the various data points required for actuator sizing:
[wptb id=25050]
(fig.1 – see table for details)
The thrust or torque values will vary depending on the design and brand of the valve. For example, a pinch valve will have a very small BTO value compared to its ETC value. Conversely, a gate valve will have a BTO value greater than the ETC. This results in dramatically different actuator sizes for fail-open applications for the same size valve.
If you have more questions about the valve signature and understanding thrust and torque values, Cowan’s valve automation experts can help you size the optimal actuator for your application.